■型創科技 / 羅偉航 應用工程師
前言
本人從事模塑行業以來,利用CAE處理過的案例和接受的技術委托中,比較難判斷的便是外觀缺陷。對於常規的CAE結果只有縫合線和包封是與外觀缺陷直接掛鈎的。而其他的如流痕、印痕等都沒有對應的結果,因此本文將以CAE分析和現場實驗結果來給讀者分享這類外觀缺陷該如何判斷。
為什麽成品會有外觀缺陷?
在此之前,我們得先弄清楚,這些缺陷是如何發生的?與之相關的因素有哪些?在參與過的客戶項目中,有時會遇到一些有趣的現象。假如你是產品設計人員,當你被告知你的產品有外觀缺陷,你可能會懷疑是不是模具設計沒做好或成型參數沒調好導致的;假如你是模具設計人員,你可能會認為產品設計不合理,試模參數不對導致的;假如你是試模人員,你調半天沒調好,你可能認為就是模具設計、產品設計的問題。每個崗位上的工程師都有自己的技術理論,最終的結果就是導向T1、T2、T3……。
其實從產品設計、模具設計、現場試模的角度來講,影響產品外觀的因素基本不會是單一的,我們可以參考表1的內容。
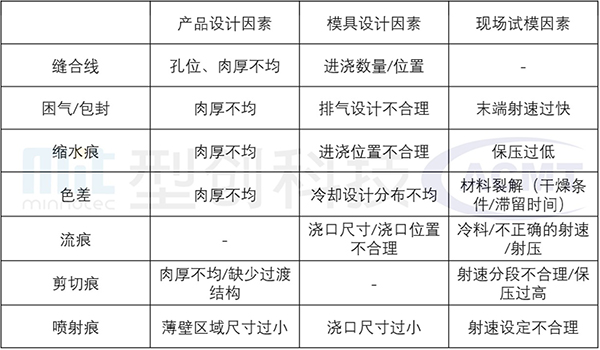
從表1中我們可以看到,很多常見的外觀問題,不一定是單一因素造成的。而我們的重點並不是把責任推給別人,而是要找到真正的問題並解决。成品的質量是與設計、材料、成型參數相互關聯的。假如設計更合理,那麽試模時的成型窗口就更寬;假如現場有完善的、科學的試模標準與性能較好的設備,那麽即使設計結構比較複雜,成型窗口較窄,我們也能找到正確的成型參數。而CAE是作為科學化、數字化設計中很重要的一樣工具。假如你是一位CAE工程師,你的困擾可能就是怎麽通過結果來判斷外觀的風險,避免重複地修模與試模。這便是本文要重點討論的內容。
通過CAE結果判斷缺陷
通過流動結果判斷缺陷
電腦試模的好處就在於無論打多大的產品,都可以輕鬆模擬塑膠流動的過程。而單看流動結果我們便可以判斷很多問題如:縫合線、流動遲滯、包封困氣、流動不平衡等。如圖1所示,通過流動結果可直接判斷該處由於兩側肉厚更大,造成熔膠流動競爭,最終形成的縫合線。從圖1右圖的實際樣品中可看到,縫合線位置相同。
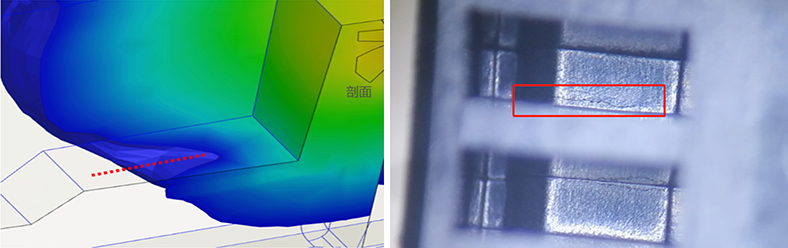
如圖2所示,該產品為3點進澆,由流動結果我們可以判斷,由於進澆數量的設計,最終會導致有多處熔膠匯合處,客戶後續也需要增加後期噴塗的成本。
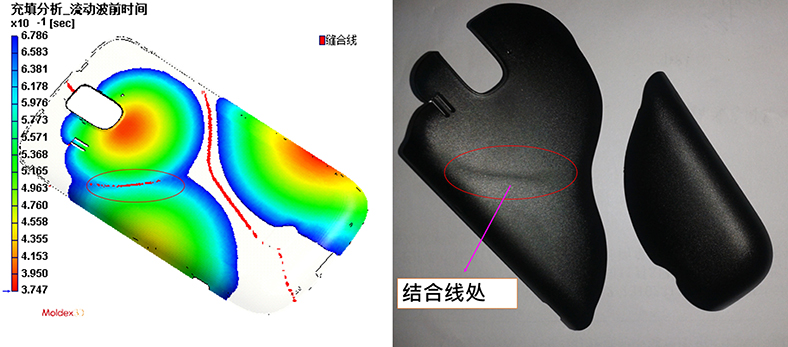
通過流動結果,還可以直接判斷該產品的肉厚分布是否合理,如圖3所示,由於圓形區域的肉厚薄,當熔膠經過此處時,流動阻力就會變大,因此更趨向於從圓形兩側流動,從而形成回包的現象。此類流動行為容易導致產品產生外觀色差。
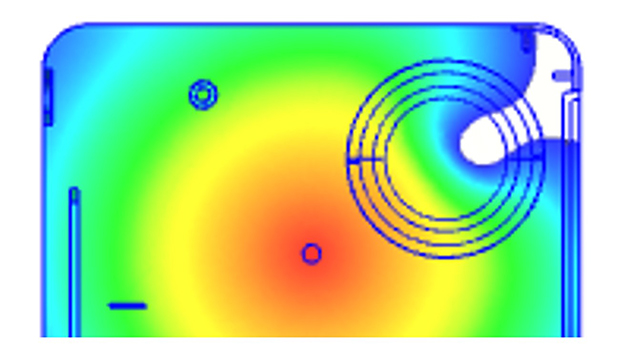
通過剪切結果判斷缺陷
剪切結果可能是CAE使用者經常會忽略的結果。相信做過CAE的讀者,都看過材料的黏度曲線(圖4)。這是一支普通熱塑性材料的黏度曲線圖。熔融塑膠基本上都屬於非牛頓型流體,也就是說液體的黏度會隨剪切速率的變化而變化。

剪切力、剪切速率可以用圖5解釋,圖5可以看成是兩塊平行的板子,而中間填充著熔融塑膠,此時向上方的木板施加一個向右的力時,速度和力會以「接力賽」的方式,一層往一層傳遞,每次傳遞都會產生速度差。加上熔膠在模穴內存在不同的散熱效果,分為了表皮層、剪切層和流動中心層,因此會存在熔膠中間速度快,兩側速度慢的「噴泉流動」(Fountain Flow)現象。
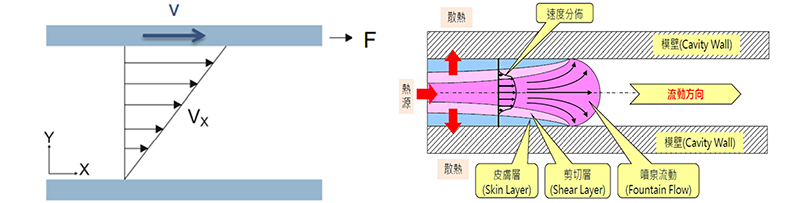
瞭解這些原理後,我們就能知道:基於熔膠的「噴泉流動」行為,當剪切越劇烈時,熔膠的速度差異越大。而不同層流的速度、溫度存在的差異就會被放大,最終變成外觀上的缺陷。而變模溫技術(RHCM),也稱急冷急熱技術,之所以能改善大多數外觀缺陷如縫合線、流痕、光澤度、色差等,主要是在高溫狀態下,改變了熔膠原本的「噴泉流動」行為,使熔膠能更平順的在模穴內流動,熔膠熔接的溫度更均勻。所以在認識熔膠流動的方式後,下面我們再來看看實例。
如應力痕的發生原因,主要是因為剪切層溫度上升,可能使原已凝固的表皮層再度軟化及熔解,甚至撑破配向的表皮層而形成有色差的應力痕。在CAE內,雖然無法呈現表皮層軟化熔解的現象,但可表現為剪切應力結果高、流動波前溫度高等結果。通過這些結果來判斷產品外觀是否有應力痕的風險。
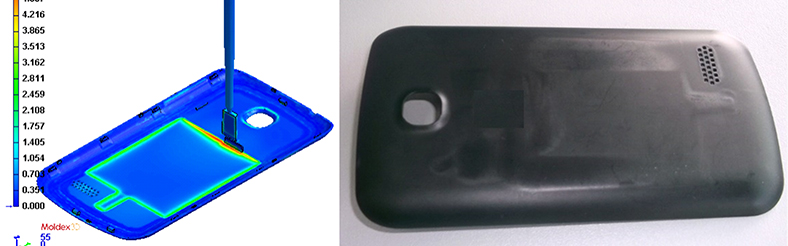
除了應力痕、還有流痕、色差、噴射痕這些在CAE上無直接結果能判斷是否存在的,我們都可以通過剪切率、速度向量、波前溫度結果,判斷是否有劇烈的速度差異、溫度差異,從而判斷是否設計有問題、是否工藝有問題。如圖7,像這種外觀有一圈像流痕的痕跡的問題,通過CAE看速度向量結果,可以看到綠色區域的一圈是速度高的地方,藍色區域是速度低的地方,此處速度的劇烈變化就有產生外觀缺陷的風險。
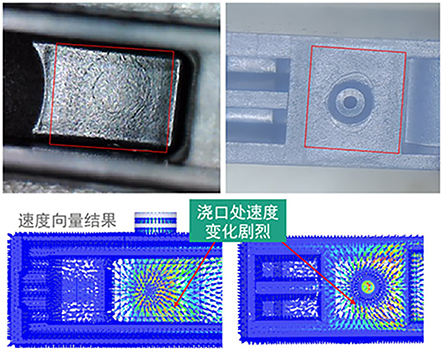
再如外觀面的白痕、色差問題,如圖8,該產品在澆口處上方的外觀面總會產生一團白痕,現場通過實驗,驗證該缺陷與模溫、射速有關係。只調整模溫的情况下,有機會改善缺陷,但仍存在輕微白痕(圖8左下),只在澆口處降速,降低剪切速率的情况下,缺陷可完美消除(圖8右下)。
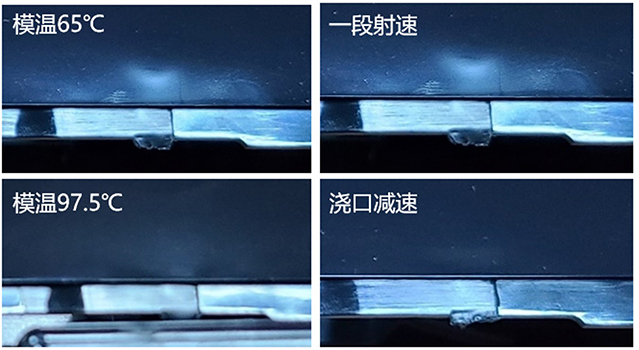
通過CAE中的剪切率結果(圖9),模擬一段射速和澆口降速的設定,結果和實際結果相似。即外觀面的速度變化越劇烈,越有產生這種外觀的色差的風險。
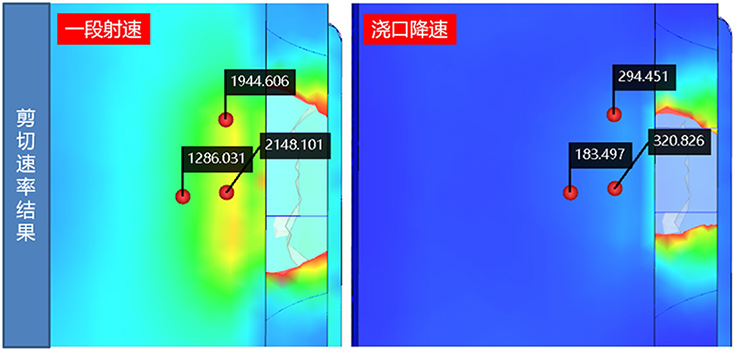
CAE結果的外觀判定標準?
很多客戶都會提出一個問題,這些CAE結果是否有固定的判定標準?比如剪切率數值在多少以內才不會有外觀問題,波前溫度在多少以內才不會有問題。像網上有流傳不同塑膠的最大剪切率數值,是不是只要CAE結果低於那個值,就不會有外觀問題呢?答案很顯然是否定的,以上所講的剪切率、速度向量、波前溫度這些CAE結果,都是通過間接方式,綜合來判斷,而不像縫合線結果可直接判斷。以應力痕為例:成型品的厚薄、射出速度的快慢,以及模溫、料溫的高低都會影響剪切層。假如你的剪切率高,但是模溫、料溫同時也控制在較高且均勻的情况下,或者產品厚薄差異不大,設計過渡合理的情况下,實際打出來的樣件可能也不會有外觀問題。
所以CAE使用者除了運用軟體,還應具備一定的產品設計、模具設計以及成型工藝能力。這樣才有利於每位CAE工程師建立屬自己的結果判定標準,比如3C產品和家電產品的標準肯定也不一樣。CAE軟體作為工具,在不同的使用者下發揮出來的價值也不同。希望這篇文章能給予工程師們一些啓發,如有不正之處,歡迎交流討論。